Cutting Costs and Enhancing Efficiency
How Heavy Machinery Manufacturers Succeed with Additive Manufacturing
The Challenge
OEMs and distributors struggle to keep 20+ year-old heavy machinery operational once the original parts are no longer available.
The Solution
OEMs and distributors utilize additive manufacturing groups to recreate the discontinued parts with additive manufacturing.
Benefits
Inventory Reduction
Material Waste Reduction
Improved Lead Times
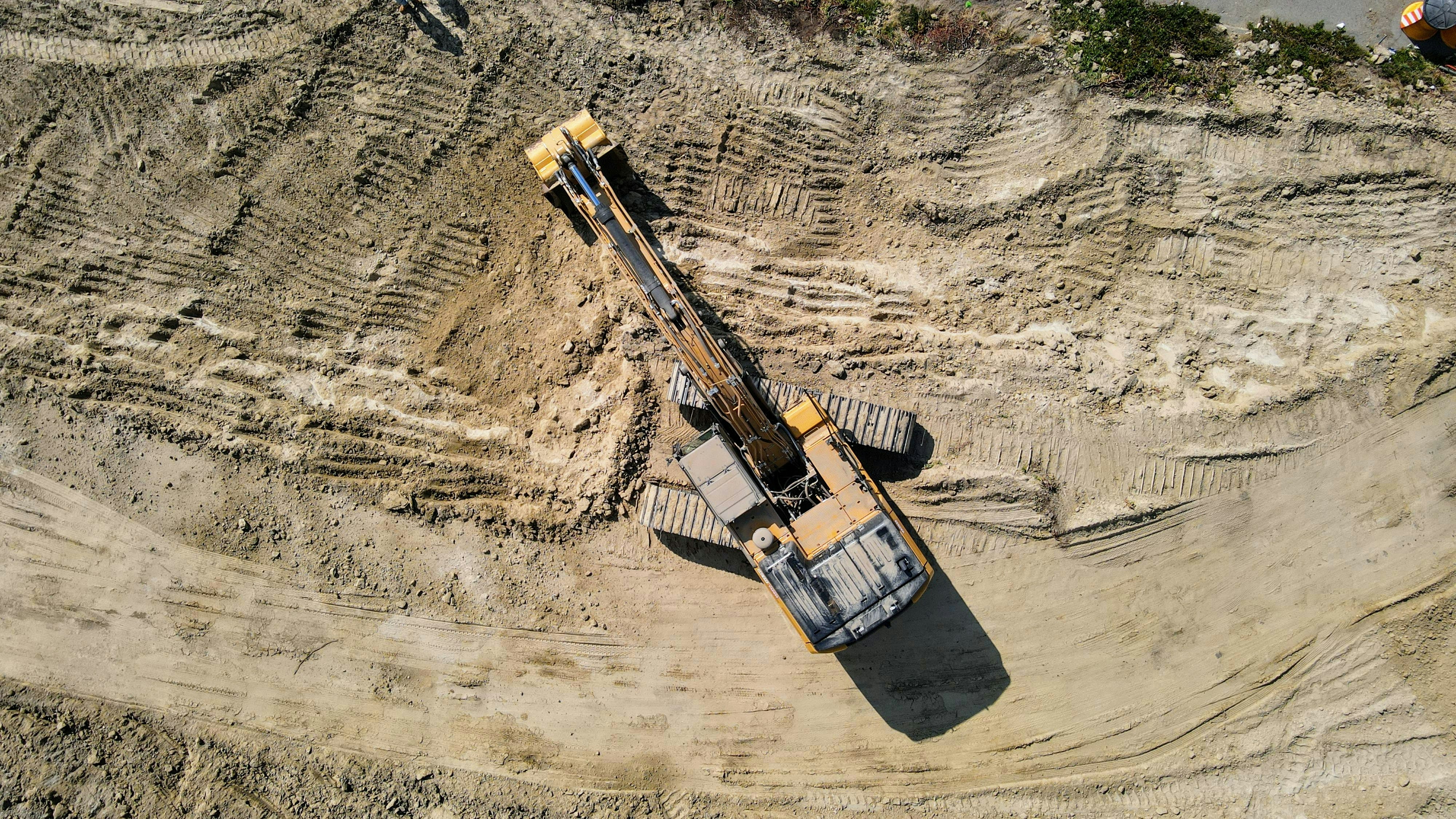
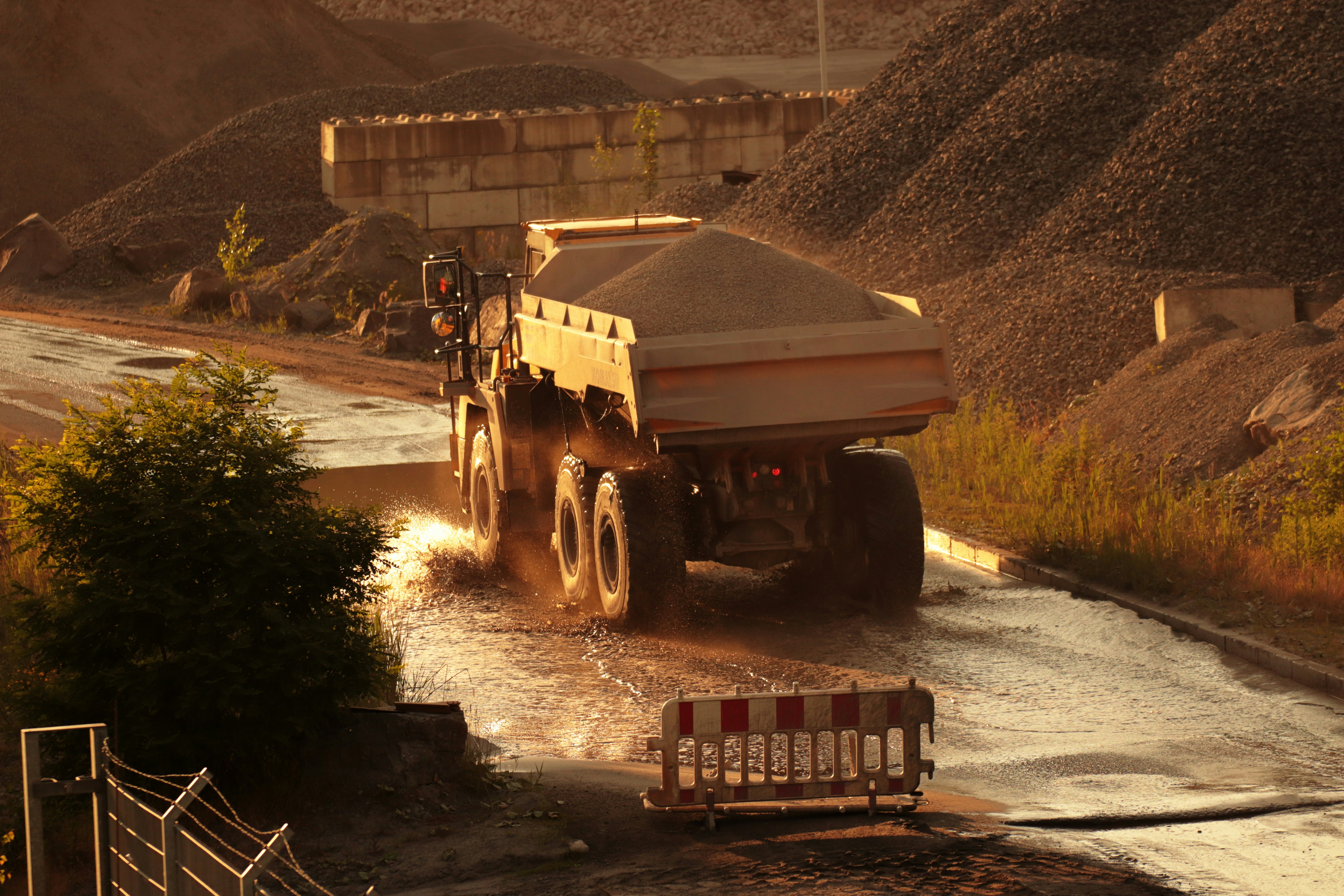
Background
OEMs and distributors struggle to keep decades-old heavy machinery running when original parts are no longer available. This often means extended downtime and higher costs for their customers, leading to frustration and dissatisfaction.
As these machines age, finding compatible parts becomes more difficult. Parts may be out of production, suppliers might be gone, or newer technology has replaced them. Traditional manufacturing methods for these discontinued parts are often expensive and slow.
Additive manufacturing (AM), or 3D printing, offers a solution to these challenges. OEMs and distributors can acquire high-quality replacement parts on-demand, reducing the need for large inventories, removing the need for capital intensive retooling, and dramatically increasing service performance. This technology enables quick production of complex parts, keeping machinery operational and efficient despite its age.
Current Challenges with Traditional Manufacturing of Replacement Parts
Expensive Production Runs
Long Lead Times
Excessive Material
Waste
Additive Manufacturing: The Solution and Its Process
Part Analysis and Digital Modeling
The original part is analyzed for its dimensions, materials, and functionality, then recreated as a 3D model using 3D scanning or CAD software to capture all the essential geometric details for 3D printing.
Material Selection
The material for the 3D printed part is carefully selected to ensure it matches the mechanical properties and performance characteristics of the original part.
Simulation and Testing
Simulations are conducted to predict the printed part's performance under different conditions, helping to identify potential issues and make adjustments before the actual printing begins.
File Preparation
The optimized digital model is converted into a 3D printer-compatible file format, such as STL or OBJ. It’s then processed through slicing software, which divides the model into layers and generates the necessary instructions for the 3D printer.
Printing and Post-Processing
The part is printed using 3D printing technology. Afterward, post-processing steps such as removing supports, sanding, or applying other treatments are performed to achieve the desired finish and properties.
Quality Assurance
The printed part undergoes inspection to ensure it meets the required specifications and quality standards. This process may include dimensional checks, material testing, and functional testing to confirm the part performs as intended.
Enduring Results
By following these steps, a traditionally manufactured part can be successfully transformed into a 3D printed design, leveraging the advantages of additive manufacturing to produce high-quality, efficient, and cost-effective replacements.
Improvement in Lead Time
Decreased Production and Inventory Costs
Increased Client Satisfaction Rates
Start Growing with Additive Manufacturing
Fill out the form and someone will reach out to you soon.