Cutting Down Costs in Manufacturing: A Data-Driven Approach
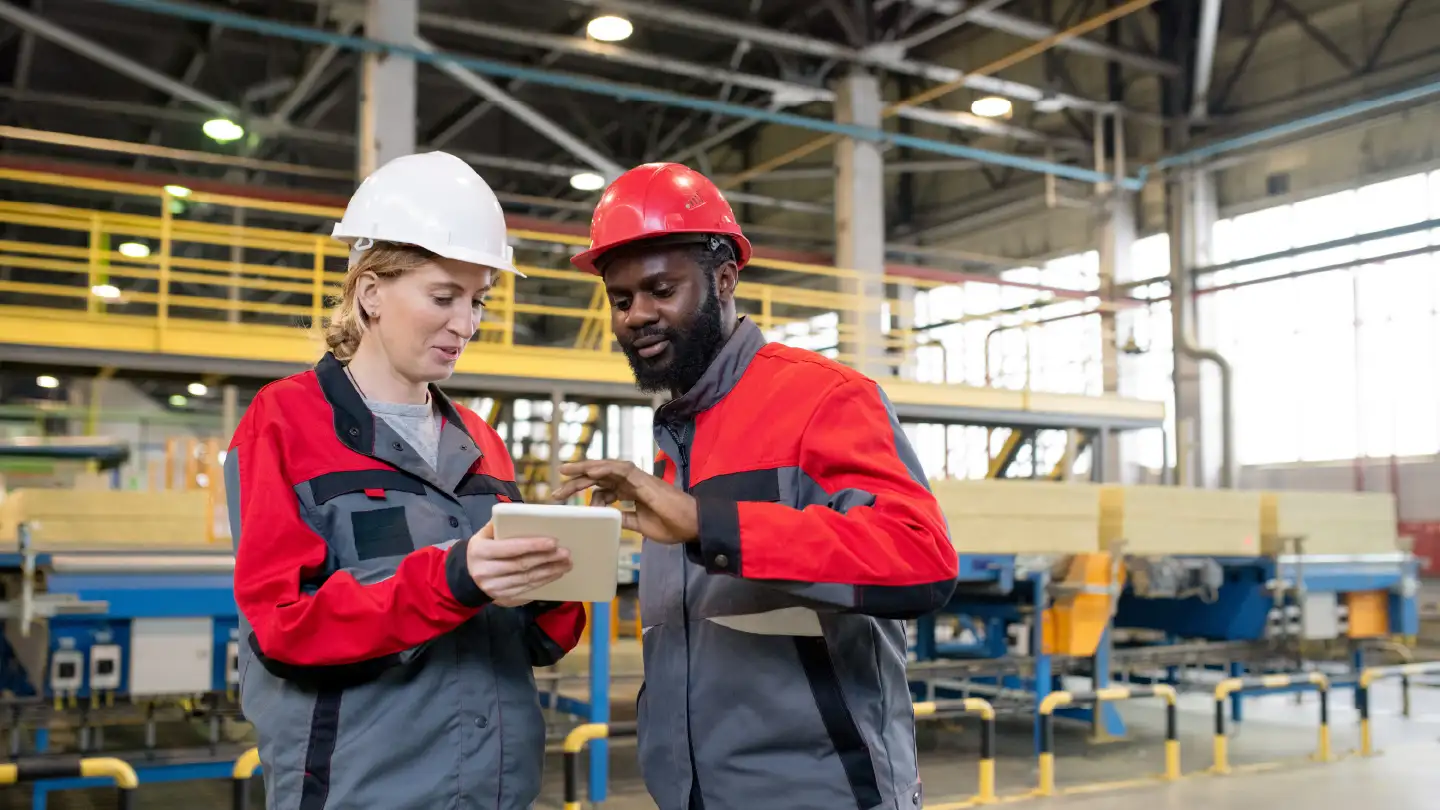
Let’s be honest—if you’re in manufacturing today, you know the game isn’t getting any easier. Margins are shrinking, supply chains are shaky, and competition is fierce. Every major manufacturer seeks an edge; the smart money is in data-driven manufacturing. It’s not a buzzword anymore; it’s the best way to cut costs while staying efficient and competitive.
Here’s the thing: data isn’t just for tech giants. It’s your ticket to streamlining your manufacturing process, reducing waste, and saving money. So, let’s talk about cutting costs using a data-driven approach.
1. Real-Time Data: Stop Guessing, Start Acting
Think about it. In the old days, manufacturers made decisions based on historical data or monthly reports, sometimes gut feelings. By the time you’ve made a change, it’s already too late. With real-time data, you’re in the driver’s seat.
Integrating IoT devices and sensors across your production line lets you gather real-time performance data on machinery, energy use, and material flow. This enables you to act immediately. Spot a bottleneck? Fix it now, not three weeks later. See a machine wearing out? Schedule maintenance before it breaks down and takes half the plant with it.
2. Predictive Maintenance: Kill Downtime Before It Kills You
Let’s talk about downtime—every manufacturer’s nightmare. A piece of machinery goes down, and the whole production line is suddenly at a standstill. Cue the panic, the delays, and the costs stacking up faster than you can say “emergency repair.”
Enter predictive maintenance. It’s like having a crystal ball but a lot more reliable. By analyzing machine data and using predictive algorithms, you can forecast equipment failure before it happens. It’s about being proactive instead of reactive.
What does that mean for you? Less downtime, fewer repairs, and way fewer headaches. Studies show predictive maintenance can reduce maintenance costs by 30% and eliminate unexpected breakdowns by 70%.
3. Inventory Management: More Science, Less Art
Inventory is one of the trickiest balancing acts in manufacturing. Too much stock? You’re eating up capital and storage costs. Too little? Your production comes to a grinding halt. And no one has time for either of those scenarios.
A data-driven inventory system solves that problem. Analyzing demand patterns, seasonality, and lead times helps you keep the right amount of stock on hand. This means you’re not wasting space and money on excess inventory and are not getting caught without the needed parts. Smart forecasting tools have helped companies cut inventory costs by as much as 50%.
4. Energy Efficiency: Your Power Bill’s Worst Nightmare
Energy is expensive, and manufacturing sucks up a lot of it. If you’re not optimizing your energy consumption, you’re leaving money on the table. Data-driven energy management tools can monitor where you’re bleeding power and suggest optimizations that save you cash.
Think of it as energy forensics. Sensors throughout your plant feed data into an energy management system that shows you what’s using the most power and when. You can adjust processes to use energy more efficiently, saving 10-30% off your energy bill.
You're falling behind if you’re not using data to drive your decisions. Ready to cut costs and boost efficiency? It’s time to go all-in on data-driven manufacturing.
What’s your next move? Keep guessing or start cutting costs the smart way?
Subscribe to our newsletter
Join our newsletter to stay up to date on features and releases.