Reviving Discontinued Parts: The Power of Additive Manufacturing in Heavy Machinery Maintenance
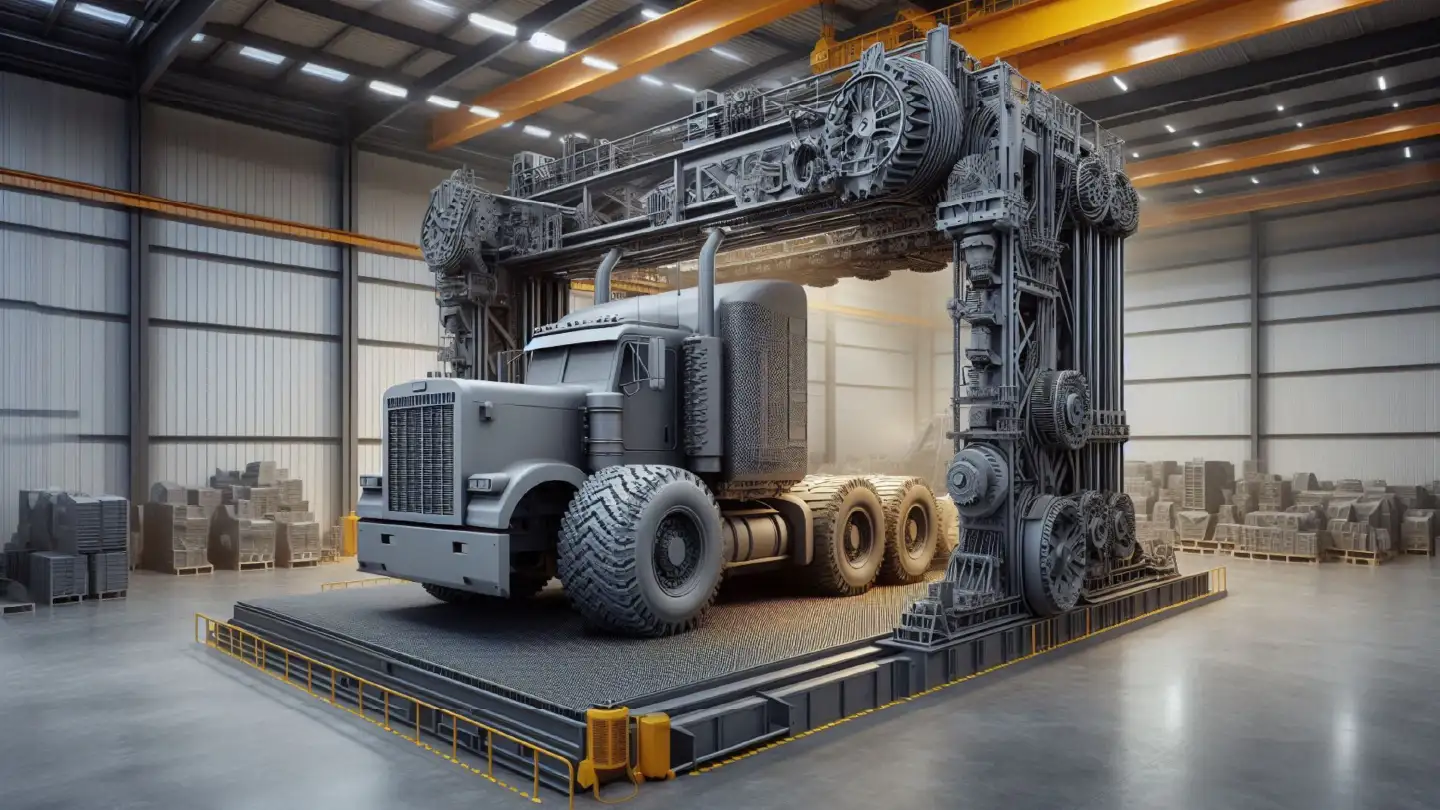
If you're in the heavy machinery industry, dealing with discontinued parts is a common frustration. Managing parts for equipment that lasts decades is challenging. Parts managers, service managers, and aftermarket sales managers at companies like Caterpillar, John Deere, and Komatsu know this well. But what if there was a solution? Enter additive manufacturing, a game-changer for this issue.
The Struggle with Discontinued Parts
Discontinued parts are a nightmare, and keeping every single part in stock for long-lasting machines isn’t practical. When a critical part becomes unavailable, it’s a huge problem. Customers with broken machines face costly downtime, which stops production and leads to significant financial losses. And let’s not even get started on how long traditional manufacturing takes to replace these parts.
What’s Additive Manufacturing?
Additive manufacturing, or 3D printing, creates objects by building them layer by layer from digital models. This technique allows for the production of complex and precise components quickly and cost-effectively. It's an excellent method for recreating discontinued parts, minimizing waste, and accelerating production timelines compared to traditional techniques.
Why Additive Manufacturing Rocks for Discontinued Parts
- Speedy and Efficient: The biggest perk? Speed. Traditional manufacturing can take months to churn out a part, especially if it’s a custom or complex design. Additive manufacturing, on the other hand, can produce parts in days or weeks. Less downtime equals happier customers.
- Cost-Effective: While 3D printed parts might cost more upfront, the overall savings are enormous for the end users. The cost of machine downtime is often way more than the part itself. By getting the part fast, you’re saving big bucks.
- Less Inventory Hassle: Keeping a vast inventory of parts is a nightmare. It’s costly and impractical. With additive manufacturing, you can produce parts on demand, which means no more massive inventories and complicated supply chains.
- Quality and Reliability: Worried about the quality of 3D printed parts? Don’t be. The tech has come a long way, and now you can get high-quality, durable parts that meet or exceed traditional standards.
- Happy Customers: Minimizing downtime and providing reliable solutions quickly is critical to keeping customers satisfied. Additive manufacturing shows you’re committed to outstanding service and innovation.
Real-World Wins
Big players in the heavy machinery world are already reaping the benefits. Caterpillar, for example, uses 3D printing to produce low-volume, high-complexity parts that you can’t get through traditional manufacturing. This helps keep their equipment running and reduces downtime for their customers.
John Deere is also on board. They use additive manufacturing to make replacement parts for older machinery models, speeding up the process and keeping their customers' equipment up and running.
Wrapping It Up
Additive manufacturing is a game-changer for dealing with discontinued parts in the heavy machinery industry. It allows for quick production of high-quality, cost-effective parts, reducing downtime, streamlining inventory management, and keeping customers happy. By embracing this technology, you can provide exceptional service and support for long-lasting equipment.
By leveraging additive manufacturing, heavy machinery manufacturers and distributors can tackle the problem of discontinued parts and pave the way for a more efficient, responsive, and customer-focused future.
Subscribe to our newsletter
Join our newsletter to stay up to date on features and releases.